How PAT tools can help improve understanding of the crystallisation process
The criticality of Crystallisation process in the manufacture of drug substances
The importance of crystallisation in the pharmaceutical and high-value chemical industries has increased recently due to many technical and commercial factors in last decade:
- Requirements to reduce impurities from quality standpoint
- Better yields from business standpoint,
- The need to crystallise difficult-to-crystallise small / macro-molecules from technical challenge standpoint
- The need to engineer specific physical property attributes from developability standpoint
- Improved downstream processability from manufacturing and cost standpoint.
These demands denote the process development is now more focused than ever before, in developing better crystallisation processes for intermediates (where impurity rejection, yield and efficient downstream processing are critical); and the final API step, where the crystallisation process is aimed to produce the final active ingredient that meets all the desired chemical and physical attributes consistently.
Crystallisation and the need of PAT tool framework
Crystallisation is one of the most important unit operations for the manufacturing of drug substances and intermediates in pharmaceutical industry. Crystallisation involves the formation of solute particles from a solution (mother liquor) under a thermodynamic driving force of supersaturation and rate kinetics of nucleation and crystal growth.
The metastable zone width (MSZW) may not be a thermodynamic property, but it is a manifestation of the ways in which the supersaturation is relieved within or outside this zone, by cooling, antisolvent addition, evaporation / distillation, and / or inducting seeding, leading to varying degrees of control on the crystallisation process design.
The crystallisation process control has significant impact on the critical quality attributes of pharmaceutical material (intermediates, API, RSMs/KSMs) such as purity, yield, crystal size distribution, solid form/polymorph, morphology and other bulk properties. However, due to complexity of the multivariate nature of pharmaceutical crystallisation process, product and process design of the pharmaceutical crystals had been empirical to a larger extent, and this led to the realisation and internalisation of science and knowledge-based strategies under the FDA’s Process Analytical Technology (PAT) Initiative.
The FDA definition of PAT is internalised in crystallisation as a system for designing, analysing and controlling crystallisation through in situ on-line monitoring of pharmaceutical processes with the goal of ensuring critical quality and performance attributes. Effective and efficient utilization of the body of scientific knowledge in a structured manner is a PAT domain.
Applicability of PAT tools in Crystallisation
PAT tools not only help to understand the process controls in terms of relieving supersaturation and hence give better control and help manage the driving force of crystallisation, but also capture visually and graphically underlying issues such as uncontrolled or crash crystallisation, oiling out phenomena, amorphous phase intermediation, solid form/polymorph conversions, secondary nucleation or fine particles generation, or processes those would adversely impact the nucleation and crystal growth/ crystallisation kinetics.
The PAT tools also help develop understanding on the mixing rate sensitivity of the process, impact of type and mechanism of the agitator and baffle hydrodynamics on the overall process CQAs, if combined well with parallel reactor workstation. The better understanding on control of crystallisation process would have a cascading impact in improving the downstream processes such as filtration, drying and milling as well.
This makes the PAT tool framework and its internalisation to crystallisation process development and monitoring a benchmark strategy to design, analyse and control crystallisation processes in the entire CMC value chain.
PAT-tool enabled crystallisation process development at Sai
At Sai, we have an excellent PAT tool set up for crystallisation process development. This includes the FBRM lasentec and the PVM probe which provide a comprehensive understanding on solubility, MSZW, nucleation point, and growth behaviour of particles during crystallisation at our Hyderabad facility.
- FBRM (Focused Beam Reflectance Measurement, Mettler Toledo) probe is inserted directly into process streams, at an angle, to ensure particles can flow easily across the probe window where the measurement takes place. It is an in-line particle formation (nucleation) and growth monitoring tool that provides the particle count in terms of chord length and chord length distribution with respect to time & temperature. This can also be used to determine solubility & MSZW.
- PVM (Particle Vision & Measurement, Mettler Toledo) enables to view and save real-time microscope-quality images of the crystals, particles, and droplets as they naturally exist in process - at dynamic & real process concentration. It corroborates information of FBRM by providing real time images and further provides additional insights on the crystal habit, morphology, secondary liquid formation and / or oiling out phenomena, polymorph monitoring, form conversions etc during the crystallisation process.
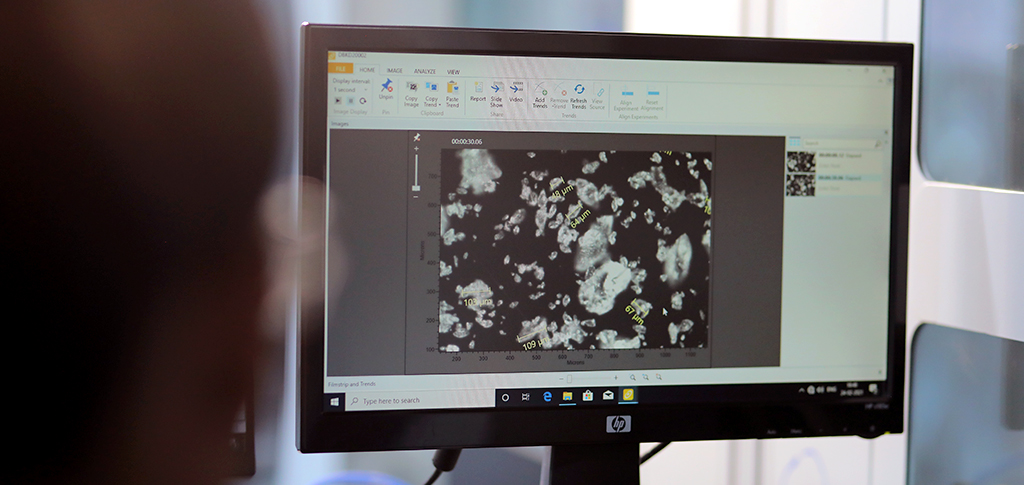
These PAT tools along with Easymax 402, Mettler Toledo, which have geometric similarity with plant scale reactors in terms of vessel geometry and impeller blades / agitators and mimic plant scale configuration, provide us a scientific set up to design crystallisation processes which have a higher probability to succeed at scale.
Apart from this Sai, has extended its PAT tool-kit capabilities to its Manchester facility as well with the introduction of the Blaze Metrics as a consolidated PAT tools that offer in-process high-resolution microscopy, particle analytics, and Raman spectroscopy in a single probe.
PAT tool in present & future R&D & Manufacturing
Effective process analytical technology (PAT) tool kit set up for online monitoring during R&D not only helps scientists design processes at lab scale with better control on particle formation and growth, but also develops confidence to take processes from lab to scale with desired yield, impurity separation/rejection and other physical property controls.
The world would see an evolution of batch to continuous mode of manufacturing, and this would mean that the process dynamics in continuous manufacturing would be by design integrated with in-situ online (PAT-enabled) monitoring of process parameters and their variabilities that may affect the quality attributes of interest or to ascertain on how the predetermined changes in process parameters and material attributes will influence the outcome of the process.